What are the quality requirements for a card and badge holder?
By APCards | Reading time : 5 minutes
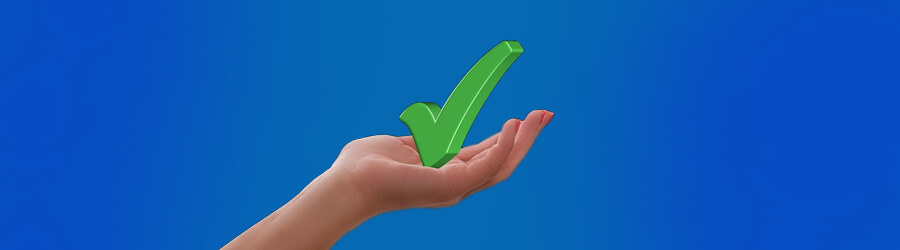
A card holder is used to protect and extend the life of the card, preventing bending, twisting and scratching which can damage the card and the information it contains.
Design is the basis for quality
In order to be durable, the card or badge holder must have a robust design, based on the simplest possible mechanical operation, with the minimum of articulated parts or parts requiring repeated movement during use.
The quality will also depend on the manufacturing and assembly method chosen at the time of design: a one-piece design is to be preferred. This can be obtained directly during moulding or just after moulding by ultrasonic welding, provided that this is controlled by the manufacturing workshop.
Material thicknesses of at least 1 mm should be used to provide sufficient durability. Below this thickness, the product will be fragile regardless of the thermoplastic material chosen. This can also be verified by the weight of the case; indeed, for equivalent dimensions (90×60 mm), the lighter the case, the more fragile it is. The minimum weight required is 12 g.
The design of the case must ensure that it is very flat in order to avoid any risk of friction when the card is inserted or removed. This risk of friction will also be limited if the case has thin guides allowing the card to slide on them, thus limiting the surfaces in contact when the card slides.
The design of the card retaining brakes is essential to ensure that the card is held securely and, if necessary, easily removed. These brakes should be progressive, allowing the card to drop easily to the bottom of the case and to be easily removed. Some models have progressive brakes that can hold contactless tickets from 0.30mm thick to 0.9mm ISO cards. They are usually referred to as “Universal” card holders.
The design of the manufacturing tools is also very important. Thus, a rheological study is essential in order to control the homogeneity of the flow when filling the material in the mould. The injection method chosen is also important in order to preserve all the initial qualities of the chosen material.
The choice of material, an important element
Each material has its own characteristics related to its composition. They differ greatly from each other and correspond to different uses.
In the case of a card holder intended to be used for several years, it is preferable to use high-end materials such as Polycarbonate or Zylar, which also offer very good transparency.
Furthermore, we strongly advise against the use of materials such as Polystyrene or PVC, which are known to be fragile to shocks and torsion when used in these thicknesses.
Choose a qualified manufacturing workshop
Choosing a quality material is essential, but it is also necessary for the transformation workshop to perfectly control all the stages of the process: preparation of the material, injection, pressure, holding, mould temperatures, cooling cycle, ejection without deformation, etc Otherwise, a well-designed part moulded in a very good material, but which is badly transformed, can lose a large part of its initial qualities.
It is therefore important to manufacture in ISO 9001 certified workshops, or even those with other levels of approval, which will guarantee maximum final product quality. These workshops generally ensure very good traceability, a guarantee of product quality and quality of material supply, by means of certificates of origin for each batch of material.
The environmental aspect can be taken into account in the quality of a case
- French manufacture limits all transport costs.
- Manufacturing in an energy approved workshop is a plus.
- A recyclable material is to be preferred.
- The existence of a collection and recycling circuit for used card holders is also an important point.
- The use of a case made of biosourced and biodegradable material is the best way to protect the environment.
- Packaging that limits the use of cardboard is also preferable.
The existence of a guarantee from the manufacturer
The existence of a written commitment from the manufacturer on a guaranteed lifetime (under normal conditions of use) can be a decisive criterion between 2 models.